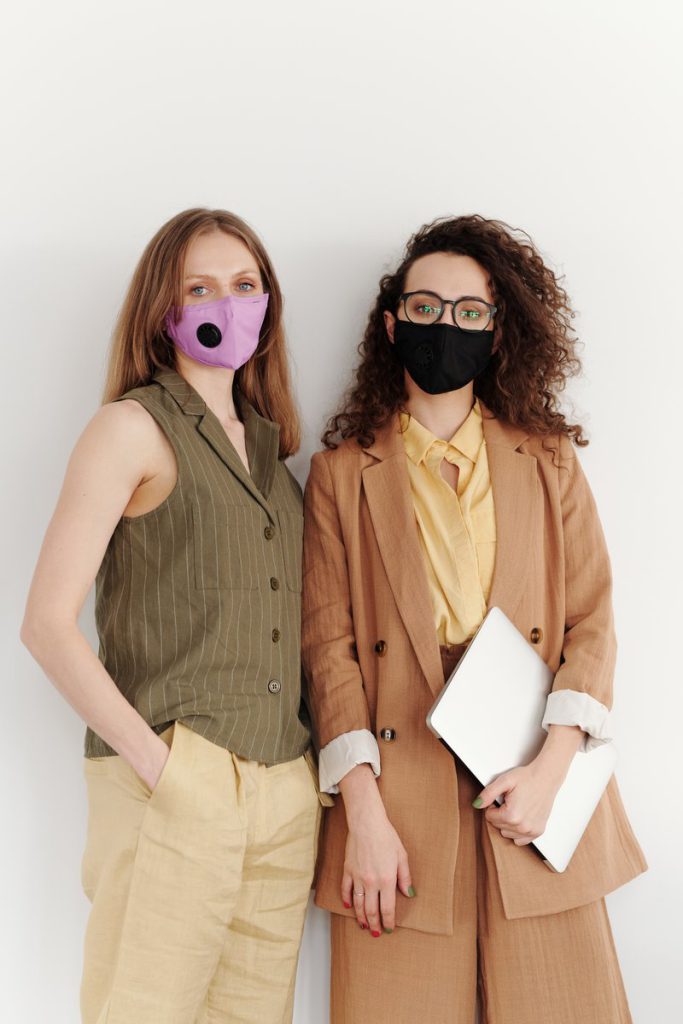
The shortage of crucial medical supplies, especially personal protective equipment, has crippled the United States’ ability to quell the COVID-19 pandemic.
At least 54,000 nursing home residents and workers have died from COVID-19 in the U.S. as of June 26. This is a staggering number when compared to nursing homes in Hong Kong, which have reported zero deaths despite cramped quarters.
Other countries with ample PPE, such as South Korea and New Zealand, have reported few deaths in nursing homes. The shortage of PPE in the United States has gone on for months and is expected to exacerbate in a second wave of COVID-19 pandemic, due to structural issues in the U.S. medical supply chain.
As an operations management scholar whose research has touched upon health care supply chains, I have been intrigued by the dire shortage of PPE. I set out to study how to make the U.S. medical supply chain more resilient and agile in a future pandemic.
In my opinion, those involved in the medical supply chain have a lot to learn from perhaps a surprising place, the fashion industry.
A lack of transparency
My study with Ge Bai and Gerard Anderson shows that the U.S. PPE supply chain suffers from a fundamental lack of transparency.
PPE manufacturers do not report supply chain information to the FDA other than the locations of their production facilities. Our extensive examination of their financial reporting didn’t turn up any quantifiable information. The media wasn’t much help, either.
PPE manufacturers also rarely report basic supply chain information to their customers. In most cases, hospitals know only the companies they directly contract with – also known as “tier-1 suppliers” – and health care providers sometimes do not know the suppliers of PPE even after delivery.
But lack of transparency is not unique to the health care industry. The fashion industry has long experienced the same pain.
Many fashion brands do not know where and how their clothes are made, because they have vast global networks of suppliers who often subcontract to other suppliers without their knowledge. Even if they do, they lack any incentive to disclose their supply chain data to the public.
After the fires
Lack of transparency kills. In Dhaka, Bangladesh, a fire in November 2012 at a garment factory killed more than 100 people, followed by another fire on April 2013 that killed more than 1,100.
These factories operate for major international brands under poor working conditions. Yet, without transparency, the public couldn’t hold brands accountable. As a result, the brands invested little in improving their suppliers’ often dangerous labor practices.
In response to the fires, the fashion industry embarked on an effort to improve supply chain transparency through the Fashion Transparency Index, which ranks major brands by how much they know about where and how their products are made and to what extent they are willing to share such information with the public.
Since its inception in 2017, the average transparency scores of the nearly 100 brands included have increased by 12 points, with more brands disclosing through corporate publications their processing facilities, raw material suppliers and other crucial supply chain information.
Preventing pandemic failures
The fashion industry has offered valuable lessons for improving the supply chain transparency.
The Fashion Transparency Index covers a wide range of performance metrics, including whether fashion brands “know, show and fix” various weaknesses of their supply chains. A transparency index for the medical supply chain might not be as comprehensive but, at a minimum, would need to measure how transparent PPE manufacturers are about their crucial supply chain information.
This level of end-to-end transparency is important because the production of specialized PPE such as N95 masks depends on crucial materials the U.S. currently has little capacity to produce.
Transparency creates an incentive for manufacturers to build domestic capacity.
Ample domestic production capacity for crucial medical supplies such as N95 masks would ensure critical raw materials, human capital and technical know-how are in place to ramp up production in times of global health emergencies.
Better end-to-end transparency of the PPE supply chain will allow governments, health care providers and the public to assess the weaknesses of the supply chain and push the manufacturers to fix them.
Tinglong Dai, Johns Hopkins University
Tinglong Dai, Associate Professor of Operations Management & Business Analytics, Johns Hopkins University
This article is republished from The Conversation under a Creative Commons license. Read the original article. https://creativecommons.org/licenses/by-nd/4.0/